ISO 18595:2021 Resistance welding — Spot welding of aluminium and aluminium alloys — Weldability, welding and testing
标准简介
Resistance welding — Spot welding of aluminium and aluminium alloys — Weldability, welding and testing是国际标准化组织(International Organization for Standardization,简称ISO)于2021-01发布的ISO标准,适用于世界范围。标准截图
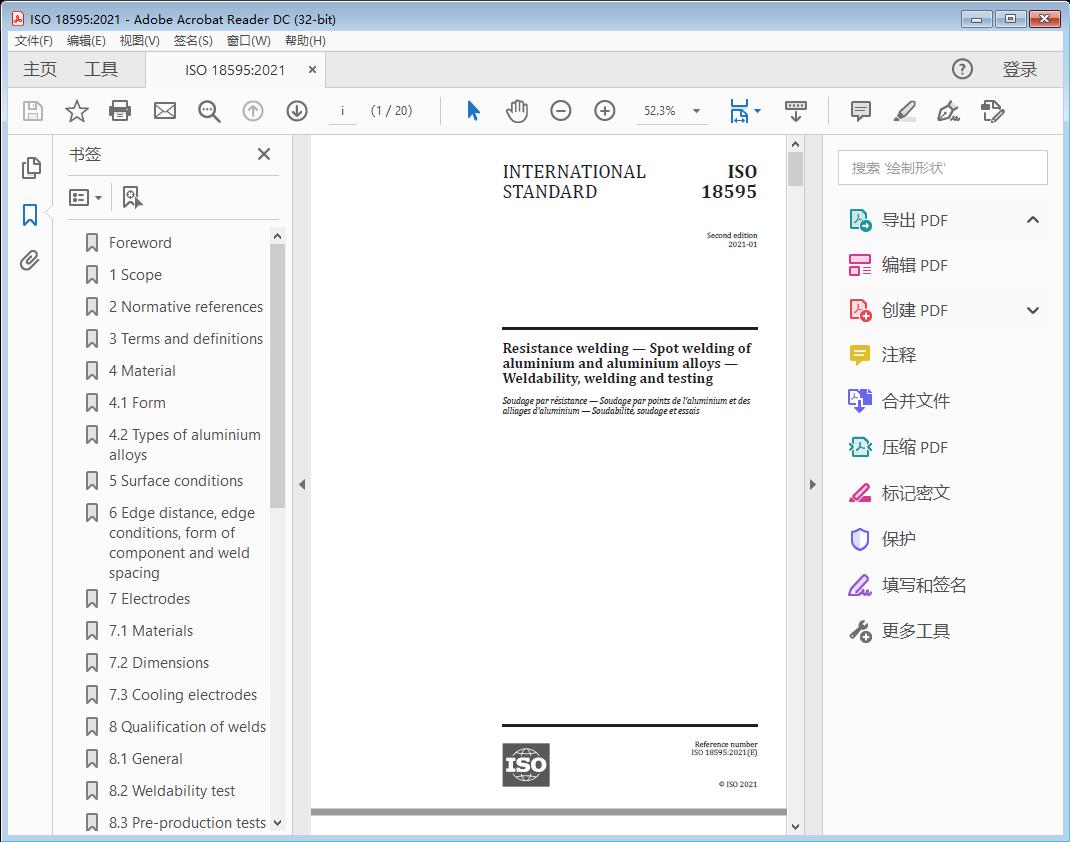
标准文档说明
标准文档类型为Resistance welding — Spot welding of aluminium and aluminium alloys — Weldability, welding and testing高清PDF版本(文字版),标准文档内可进行搜索,可以复制原文,可粘贴。标准部分原文
Resistance welding — Spot welding of aluminium and aluminium alloys — Weldability, welding and testing
1 Scope
This document specifies requirements for resistance spot welding in the fabrication of assemblies of aluminium sheet, extrusions (both work- and age-hardening alloys) and/or cast material comprising two or three thicknesses of metal, where the maximum single (sheet) thickness of components to be welded is within the range 0,6 mm to 6 mm.
This document is applicable to the welding of sheets or plates of dissimilar thickness where the thickness ratio is less than or equal to 3:1. It applies to the welding of three thicknesses where the total thickness is less than or equal to 9 mm.
Welding with the following types of machines is within the scope of this document:
— pedestal welding machines;
— gun welders;
— automatic welding equipment where the components are fed by robots or automatic feeding equipment;
— multi-welders;
— robotic welders.
Information on appropriate welding equipment is given in Annex A and on spot welding conditions in Annex B. The latter are for guidance only and can require modification depending on service conditions of the fabrication, type of welding equipment, characteristics of the secondary circuit, electrode material and geometry.
The welding of coated material, e.g. zinc-coated or anodized material, is outside the scope of this document.
2 Normative references
The following documents are referred to in the text in such a way that some or all of their content constitutes requirements of this document. For dated references, only the edition cited applies. For undated references, the latest edition of the referenced document (including any amendments) applies.
ISO 209, Aluminium and aluminium alloys — Chemical composition
ISO 669, Resistance welding — Resistance welding equipment — Mechanical and electrical requirements
ISO 3522, Aluminium and aluminium alloys — Castings — Chemical composition and mechanical properties
ISO 5182, Resistance welding — Materials for electrodes and ancillary equipment
ISO 5184, Straight resistance spot welding electrodes
ISO 5821, Resistance welding — Spot welding electrode caps
ISO 5830, Resistance spot welding — Male electrode caps
ISO 10447, Resistance welding — Testing of welds — Peel and chisel testing of resistance spot and projection welds
ISO 14273, Resistance welding — Destructive testing of welds — Specimen dimensions and procedure for tensile shear testing resistance spot and embossed projection welds
ISO 15614-12, Specification and qualification of welding procedures for metallic materials — Welding procedure test — Part 12: Spot, seam and projection welding
ISO 17677-1, Resistance welding — Vocabulary — Part 1: Spot, projection and seam welding
ISO 18278-2, Resistance welding — Weldability — Part 2: Evaluation procedures for weldability in spot welding
3 Terms a nd definiti ons
For the purposes of this document, the terms and definitions given in ISO 669 and ISO 17677-1 apply.
ISO and IEC maintain terminological databases for use in standardization at the following addresses:
— ISO Online browsing platform: available at https:// www .iso .org/ obp
— IEC Electropedia: available at http:// www .electropedia .org/ 4 Material
4.1 Form
The material shall be according to ISO 209 and ISO 3522.
4.2 Types of aluminium alloys
A partial list of aluminium alloys is given in Annex C.
5 Surface conditions
Prior to welding, all surfaces shall be checked for their suitability for spot welding. The surfaces should preferably be free from oil, grease, lubricant, visible oxidation, paint, dirt or excessive scratches. If necessary, appropriate surface treatment, e.g. chemical etching, shall be carried out. Unless specifically developed for spot welding, mill-finish surfaces are generally not suitable for spot welding and can need pre-treatment. Die-cast material shall be free from excessive surface roughness and imperfections, e.g. as caused by washing out of the die material. Aluminium manufacturers and component suppliers can produce surface-treated material suitable for spot welding, e.g. with TiZr conversion coating. In addition, coated material can be supplied with chromate or phosphate passivation. Phosphated aluminium may be used in certain applications. Excessive quantities of dissolved gases in die-cast material shall be avoided. These materials can be spot welded, although adjustment of the welding parameters is generally necessary as outlined in Annex B.
In all cases, the surface condition and any surface treatment shall be recorded in the testing documentation.
The stability of surface condition can be evaluated by measuring the transition resistance in accordance with ISO 18594.
6 Edge distance, edge conditions, form of component and weld spacing
The components to be welded shall be free from burrs or other defects, which can, in any way, interfere with interface contact or require excessive force to fit the parts together.
网盘链接
百度网盘:https://pan.baidu.com/s/1Z2VzPHBe_bACpmC0Pp_o9w
提取码:9eaq
【温馨提示】大资料ISO是提供信息发布的专业信息类网站,所有内容均由用户发布,不代表本站观点,本站亦不存储所涉及的文件及资料。如有【免费资料】以及【付费资料】,请用户根据自己的需求,自行判断是否需要获取。如有交易诈骗、内容侵权可发送邮件至kf@dzl100.com,我们审查后若发现情况属实,会立即对相关内容进行删除处理。
加载用时:48.009 毫秒
相关评论
相关文章
-
ISO 18595:2021 Resistance welding — Spot welding of aluminium and aluminium alloys — Weldability, welding and testing
Resistance welding — Spot welding of aluminium and aluminium alloys — Weldability, welding and testing是国际标准化组织(International Organization for Standardization,简称ISO)于2021-01发布的ISO标准,适用于世界范围。本次分享的标准文档为高清PDF(文字版),标准文档内可搜索,可复制,可粘贴。本文结尾附网盘链接。
-
ISO 10014:2021 Quality management systems — Managing an organization for quality results — Guidance for realizing financial and economic benefits
Quality management systems — Managing an organization for quality results — Guidance for realizing financial and economic benefits是国际标准化组织(International Organization for Standardization,简称ISO)于2021-04-20发布的ISO标准,适用于世界范围。本次分享的标准文档为高清PDF(文字版),标准文档内可搜索,可复制,可粘贴。本文结尾附网盘链接。
-
ISO 19475:2021 Document management — Minimum requirements for the storage of documents
Document management — Minimum requirements for the storage of documents是国际标准化组织(International Organization for Standardization,简称ISO)于2021‑06‑10发布的ISO标准,适用于全球。本次分享的标准文档为高清PDF(文字版),标准文档内可搜索,可复制,可粘贴。本文结尾附网盘链接。
-
ISO 19206-3:2021 Road vehicles — Test devices for target vehicles, vulnerable road users and other objects, for assessment of active safety functions —Part 3: Requirements for passenger vehicle 3D targets
Road vehicles — Test devices for target vehicles, vulnerable road users and other objects, for assessment of active safety functions —Part 3: Requirements for passenger vehicle 3D targets是ISO于2021‑05‑21发布的ISO标准,适用于全球范围。本次分享的标准文档为高清PDF(文字版),标准文档内可搜索,可复制,可粘贴。本文结尾附网盘链接。
-
Petroleum and natural gas industries — Site-specific assessment of mobile offshore units —Part 3: Floating units
Petroleum and natural gas industries — Site-specific assessment of mobile offshore units —Part 3: Floating units是国际标准化组织(International Organization for Standardization,简称ISO)于2021-03发布的ISO标准,适用于国际,世界范围。本次分享的标准文档为高清PDF(文字版),标准文档内可搜索,可复制,可粘贴。本文结尾附网盘链接。
-
ISO 16355-1:2021 Application of statistical and related methods to new technology and product development process —Part 1: General principles and perspectives of quality function deployment (QFD)
Application of statistical and related methods to new technology and product development process —Part 1: General principles and perspectives of quality function deployment (QFD)是ISO于2021-05发布的ISO标准,适用于世界范围。本次分享的标准文档为高清PDF(文字版),标准文档内可搜索,可复制,可粘贴。本文结尾附网盘链接。
-
ISO 16140-3:2021 Microbiology of the food chain — Method validation —Part 3: Protocol for the verification of reference methods and validated alternative methods in a single laboratory
Microbiology of the food chain — Method validation —Part 3: Protocol for the verification of reference methods and validated alternative methods in a single laboratory是国际标准化组织于2021-01发布的ISO标准,适用于全球。本次分享的标准文档为高清PDF(文字版),标准文档内可搜索,可复制,可粘贴。本文结尾附网盘链接。
-
ISO 10140-1:2021 Acoustics — Laboratory measurement of sound insulation of building elements —Part 1: Application rules for specific products
Acoustics — Laboratory measurement of sound insulation of building elements —Part 1: Application rules for specific products是国际标准化组织(International Organization for Standardization,简称ISO)于2021-05发布的ISO标准,适用于世界范围。本次分享的标准文档为高清PDF(文字版),标准文档内可搜索,可复制,可粘贴。本文结尾附网盘链接。
-
ISO 16321-1:2021 Eye and face protection for occupational use —Part 1: General requirements
Eye and face protection for occupational use —Part 1: General requirements是ISO于2021-03发布的ISO标准,适用于全球。本次分享的标准文档为高清PDF(文字版),标准文档内可搜索,可复制,可粘贴。本文结尾附网盘链接。
-
ISO 11665-4:2021 Measurement of radioactivity in the environment — Air: radon-222 —Part 4: Integrated measurement method for determining average activity concentration using passive sampling and delayed analysis
Measurement of radioactivity in the environment — Air: radon-222 —Part 4: Integrated measurement method for determining average activity concentration using passive sampling and delayed analysis是国际标准化组织于2021-03发布的ISO标准,适用于全球。本次分享的标准文档为高清PDF(文字版),标准文档内可搜索,可复制,可粘贴。本文结尾附网盘链接。
-
ISO 10315:2021 Cigarettes — Determination of nicotine in total particulate matter from the mainstream smoke — Gas-chromatographic method
Cigarettes — Determination of nicotine in total particulate matter from the mainstream smoke — Gas-chromatographic methodWARNING — The use of this document can involve hazardous materials, operations and equipment. This document does not purport to address all the safety problems associated with its use. It is the responsibility of the user of this document to establish appropriate safety and health practices and determine the applicability of any other restrictions prior to use.是国际标准化组织(Interna
-
ISO 14644-17:2021 Cleanrooms and associated controlled environments —Part 17: Particle deposition rate applications
Cleanrooms and associated controlled environments —Part 17: Particle deposition rate applications是国际标准化组织于2021-02发布的ISO标准,适用于全球范围。本次分享的标准文档为高清PDF(文字版),标准文档内可搜索,可复制,可粘贴。本文结尾附网盘链接。
-
ISO 17226-1:2021 INTERNATIONAL STANDARDIULTCS/IUC 19-1:2021(E)Leather — Chemical determination of formaldehyde content —Part 1: Method using high-performance liquid chromatography
INTERNATIONAL STANDARDIULTCS/IUC 19-1:2021(E)Leather — Chemical determination of formaldehyde content —Part 1: Method using high-performance liquid chromatography是国际标准化组织于2021-02发布的ISO标准,适用于国际范围。本次分享的标准文档为高清PDF(文字版),标准文档内可搜索,可复制,可粘贴。本文结尾附网盘链接。
-
ISO 19290:2021 Cigarettes — Determination of tobacco specific nitrosamines in mainstream cigarette smoke — Method using LC-MS/MS
Cigarettes — Determination of tobacco specific nitrosamines in mainstream cigarette smoke — Method using LC-MS/MS是国际标准化组织于2021-02发布的ISO标准,适用于国际范围。本次分享的标准文档为高清PDF(文字版),标准文档内可搜索,可复制,可粘贴。本文结尾附网盘链接。
-
ISO 10140-4:2021 Acoustics — Laboratory measurement of sound insulation of building elements —Part 4: Measurement procedures and requirements
Acoustics — Laboratory measurement of sound insulation of building elements —Part 4: Measurement procedures and requirements是ISO于2021-04发布的ISO标准,适用于全球范围。本次分享的标准文档为高清PDF(文字版),标准文档内可搜索,可复制,可粘贴。本文结尾附网盘链接。